Cutting Edge Remote Scanning, Diagnostics, ADAS Calibration & Programming Services
Diagnostics, Programming & Calibrations – It’s all we do!
AirPro Diagnostics is the most advanced, remote diagnostics, calibration, and programming services on the market today! AirPro utilizes OEM software as well as comprehensive multi-brand diagnostic applications directly connected to the vehicle, or local, as some vehicle manufacturers require, while remotely operated by a skilled, brand specialist team of expert diagnosticians. Our service is truly touch-free and minimizes the risk of additional outside contagions entering your facility.
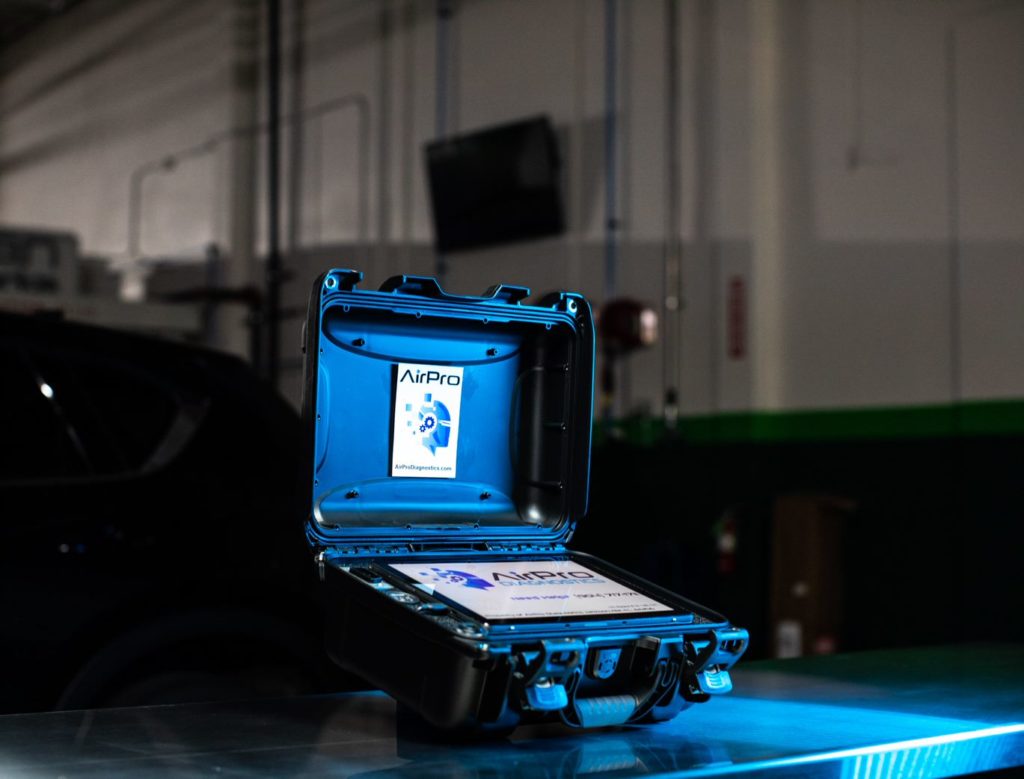
Complete End-to-End Solutions
for Collision, Glass, and Repair Shops
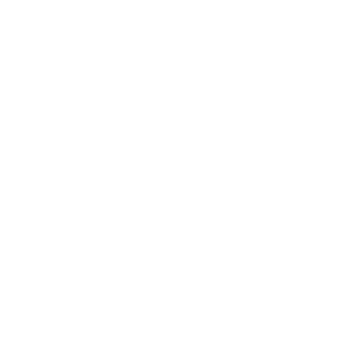
SCANNING
Comprehensive scanning by vehicle brand specialists
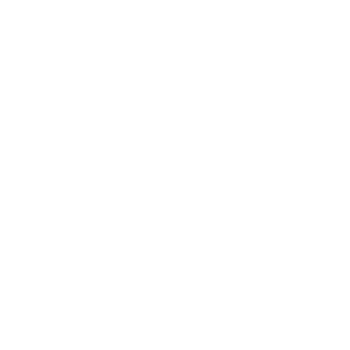
DIAGNOSTICS
Pinpoint diagnostics in real time by reading live data
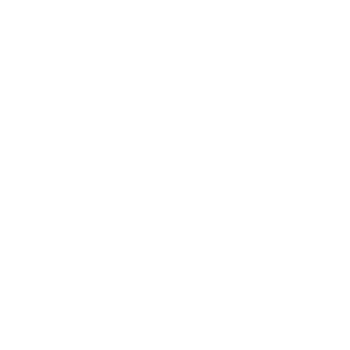
PROGRAMMING
Brand-specific module programming at your fingertips
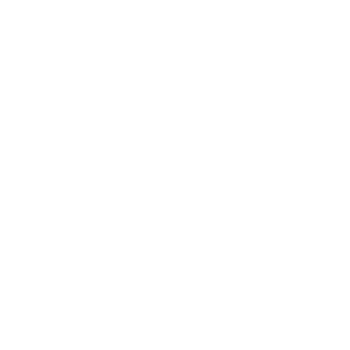
CALIBRATIONS
Keep ADAS calibrations in-house utilizing AUGGIE
Remote Scanning, Diagnostics, ADAS Calibration & Programming Services FAQs
- catch any additional repair issues to include in a comprehensive repair plan/estimate for your customers
- reduce cycle time, which will allow you to satisfy customers while expanding your repair capacity
- Improve quality control, further enhancing your shop’s reputation
- provide the ultimate in:
- vehicle safety before cars go back on the road
- quality as you repair to manufacturer’s specifications
- customer satisfaction
The recalibration process focuses on the camera-based sensors in a vehicle that sense and gather data to forward to the car’s advanced driver assistance systems (ADAS). In newer vehicles, the sensors are at their optimal factory settings in precise positioning. Over time, sensor positioning can shift—whether that’s because of fender benders or windshield replacement– many instances require a recalibration. And, in a collision with structural damage, the 4-wheel alignment must be corrected which then necessitates a Forward-Facing Camera (FFC) recalibration.
When these sensors are just slightly off, they can cause significant problems with maneuverability and driver safety—with more serious misalignment causing even bigger problems. ADAS FFC calibration involves realignment that returns the vehicle to original specifications.
Performing ADAS Calibrations today just got much simpler with AirPro’s AUGGIE DTS (Digital Targeting System). Auggie DTS replaces physical targets with digitized, miniaturized targets presented to the FFC in a theater-like environment for portable, quick, and accurate FFC calibrations. The Auggie now works with any scan tool that has calibration capabilities.
With AirPro tools and brand specialists, you can seamlessly add ADAS calibrations into your shop workflow. Benefits include the following:
- managing radar, FFC, 360 camera, blind spot ADAS calibrations in-house.
- expanding your service offerings
- speeding up the repair process
- adding a new revenue stream
- contributing to your bottom line
- removing space constraints
Experts agree that AUGGIE DTS is a genuine game changer, allowing shops to correctly calibrate cars and get them safely back on the road as quickly as possible, without sending calibrations out or calling a mobile vendor. AirPro efficiently provides what you need for radar, blind spot, and forward-facing camera calibrations in one package. Plus, you’ll receive clear procedures for your team—whether they’re new on the job or already experienced—that remove the guesswork.
To discuss how our world-class ADAS calibration technology can enhance your shop, please contact us online or call 904-717-1711.